When it comes to floor coatings, durability is paramount. Whether it’s for your garage, workshop, or commercial space, you want a solution that not only looks great but also withstands the test of time. From traditional latex paint to more advanced epoxy options, the market offers various choices, each with its own set of pros and cons. However, in recent years, polyaspartic concrete coatings have emerged as the gold standard for longevity and resilience, revolutionizing the industry.
Over the course of the thousands of coatings we do on concrete floors, some of the most common questions we get at Floor Shield are, “Are polyaspartic concrete coatings long-lasting?” and “How much longer do they last compared to the alternatives?”
We’ll answer these questions honestly, giving you a transparent layout of what you can expect from not only polyaspartic coatings but other concrete coatings too. Let’s break down the lifespan of various floor coatings to understand why polyaspartic coatings stand out:
- Latex Paint:
This is perhaps the most common and budget-friendly option for floor coatings. However, its longevity is severely limited, typically lasting no more than a couple of years. Latex paint only colors your concrete. It lacks protective properties, making it prone to chipping and wear, especially in high-traffic areas.
Floor paint is the least expensive option, and it is far more DIY-friendly than the alternatives, but you’ll have to repaint your floor often.
- Cheap Epoxy Kits:
While slightly more durable than latex paint, cheap epoxy kits available at retail stores still offer limited longevity, usually lasting a few years at best. For garage floors, the difference between paint and cheap epoxy isn’t substantial, making paint the more cost-effective option.
If you want to go with an epoxy coating, we recommend going with a company that specializes in installing concrete coatings. Make sure they aren’t using a low-quality epoxy and are cleaning/prepping your surface properly. You can use our Floor Shield installation process below as a general guide to what you should expect.
Floor Assessment:
- Conduct comprehensive assessments of the floor, including evaluations of hardness and moisture levels.
- Utilize a Mohs test to gauge concrete hardness by performing scratch tests, informing recommendations for optimal grinding pads.
- Employ a moisture meter to ascertain the moisture content of the concrete surface.
Surface Protection:
- Protect surrounding areas such as driveways and sidewalls to prevent spillage of products.
- Utilize materials like Ram Board or equivalents to shield non-targeted surfaces from damage.
Crack Repair:
- Identify and patch all cracks in the concrete to ensure a seamless surface.
Concrete Grinding:
- Grind the concrete surface to achieve uniformity. This process enhances product adherence by profiling it and removing “bond breakers” like oil and dirt.
- Note: While some companies may choose acid etching for time and cost efficiency, it can lead to uneven surfaces and damage the concrete’s lifespan.
Dust Elimination:
- Thoroughly remove silica or dust particles from the floor to prepare it for subsequent steps, crucial for proper adhesion.
Moisture and Softness Management:
- If necessary, address issues with soft concrete by taking steps to harden it.
- Apply a moisture-vapor barrier coating if excessive moisture is present to prevent coating failure.
- Level the concrete as needed, potentially extending the project timeline.
Color Coat Application:
- Apply the color coat onto the prepared concrete surface.
Flake Application:
- Disperse flakes over the color coat to achieve an appealing aesthetic and provide additional protection.
Clear Coat Finish:
- Apply a clear coat to safeguard the flakes and enhance the floor’s appearance with a glossy finish.
Cleanup:
- Thoroughly clean the work area to leave it in a better condition than at the project’s start.
- Concrete Stain:
In terms of longevity, the next best thing is concrete stains, which last around 5 years. While they provide some water-repellent properties by seeping into the concrete’s pores during application, they’re not highly protective against abrasion or heavy traffic.
- Polished Concrete:
Polished concrete lasts roughly 5 – 7 years depending on the level of traffic it receives. Polished concrete is not common in garages because it tends to not only be slicker than other coating options but it’s also weak to:
- Hot-tire pickup
- Road salts
- Abrasion
Polished concrete will wear down quickly in high-traffic settings, especially where vehicles drive over it regularly. However, polished concrete is easy to repair. This is why many retail stores use it, as they can just repolish every couple of years at a relatively low cost.
- Polyurea Coatings:
Offering a lifespan of 7 to 10 years, polyurea coatings excel in flexibility and durability. Polyurea is very flexible, meaning it can move with the natural movements of the earth to prevent cracking and breaking. Polyureas are also stronger than typical epoxies, making them durable against abrasion.
However, like all the previous options on this list, polyureas are prone to UV damage. Meaning if they get frequent sunlight, they will:
- Fade
- Yellow
- Break down
This is why installers must put so many flakes in polyurea coatings, because if they don’t, the yellowing will be more exaggerated. Additionally, the flakes protect the base coating from failing faster.
Nowadays, you’ll rarely see garages coated with epoxies, they’ll almost always be a polyurea base coat with a polyaspartic topcoat. This is because epoxies break down in sunlight even faster than polyurea. Most every polyurea floor has a polyaspartic topcoat because polyaspartic coatings are not only completely UV stable but are more durable than polyureas.
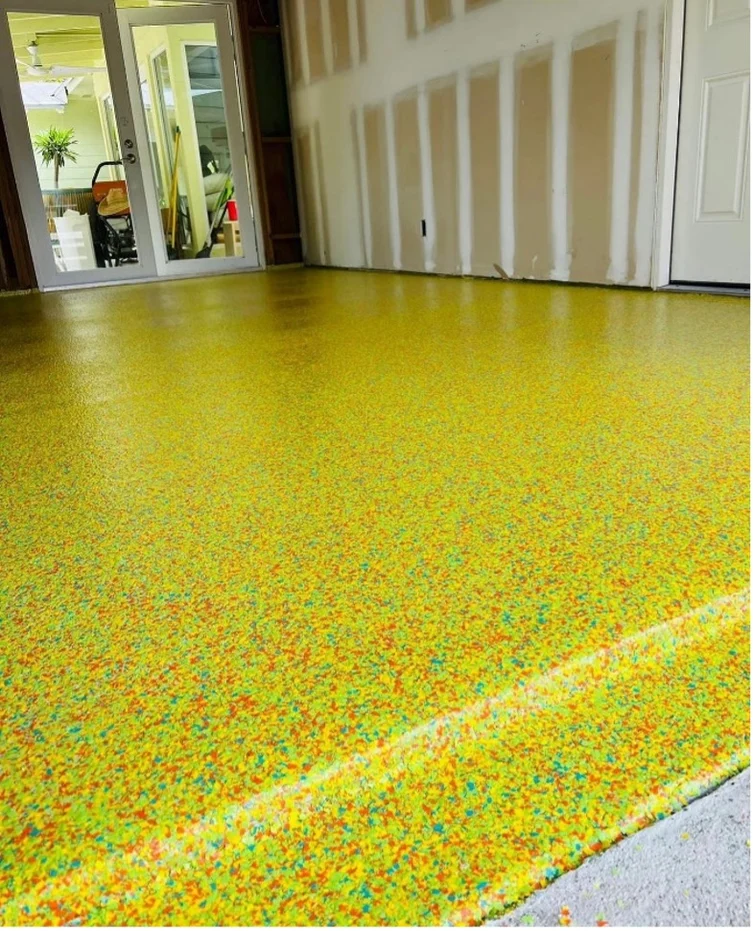
- Polyaspartic Coatings:
Polyaspartics are hailed as the most robust coatings in the industry, boasting unparalleled longevity and resilience. With a lifespan of 15 years or more, polyaspartic coatings are completely UV stable, meaning they won’t fade or deteriorate under sunlight. This makes them ideal for outdoor applications like garage floors.
At Floor Shield, we stand behind our 100% polyaspartic coating with a 15-year non-prorated warranty. Unlike other coatings, our warranty coverage remains consistent over the entire 15 years, reflecting our confidence in the longevity and performance of our product. We work on thousands of floors every year and go back to ones we’ve worked on years ago that look the same as when we first installed our coating.
Moreover, the integrity of the coating system relies on each component functioning properly. Even a minor flaw can compromise the entire coating’s performance. An example of this is a story of one of our dealers whose previous work had him use subpar flakes. Not long after his installations, the UV-stable clear coats would change color. He didn’t understand why.
We investigated the problem and found that it was due to his flakes not being UV stable, so they had lightened significantly. The clear coat was unchanged, it just didn’t appear that way because the flakes had changed so much and were affecting the look of the rest of the coating.
Conclusion
When it comes to floor coatings, your choice will depend on weighing cost and longevity. Traditional options like latex paint and cheap epoxy offer cheaper, temporary solutions, but investing in polyaspartic coatings provides unmatched durability and longevity.
If you’d like to get a free, no-obligation quote for Floor Shield’s 100% polyaspartic concrete coating, fill out the form below.